Pelletgyártás A pellet a megújuló energiák egyik egyre jobban elterjedő fajtája, amely nagy előnye, hogy hulladékokat, melléktermékeket dolgoz fel és alakítja át azokat értékes termékké, vagyis földrajzilag és gazdaságilag elérhető, biztonságos és komfortos, környezetbarát energiahordozóvá. A gyártás folyamata: 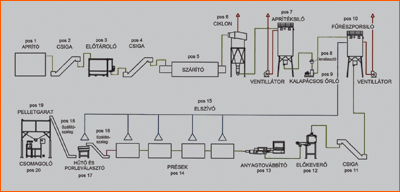 A telephelyre beszállított alapanyag – amennyiben nem megfelelő a szemcsemérete – először az aprítógépbe (pos 1) kerül, ahonnan csigás anyagtovábbítóval az előtárolóba (pos 3) jut. Az előtárolónak az a feladata, hogy olyan puffertárolót képezzen a szárító (pos 5) előtt, ahonnan biztosítható a nedves alapanyag (a szárítás utáni nedvességtartalom változásának függvényében), a folyamatosan változó tömegáramú anyagbehordás a szabályozott fordulatszámú csigás kihordóval (pos 4) a szárítóba. A szárítóközeget (forró levegő vagy füstgáz) és a szárítandó anyagot a ciklon ventilátora (pos 6) mozgatja át a szárítón. A nagy sebességű légáram magával sodorja a száraz szemcséket, amelyek a ciklonba jutva – mivel az áramlási keresztmetszet hirtelen kitágul és az áramlási sebesség lecsökken – különválnak, és a száraz alapanyag a ciklon aljába esik, ahonnan cellás adagolóval történik a kitárazás. Innen szintén pneumatikus szállítással jut az úgynevezett aprítéksilóba, ahonnan először egy mágneses leválasztóba (pos 8), majd a kalapácsos őrlőbe (pos 9) kerül, hogy a már száraz alapanyagot a pelletálásnoz szükséges 2-4 mm-es szemcsenagyságúra darálja. A kalapácsos őrlőből (továbbra is légszállítással) az alapanyag a fűrészporsilóba (pos 10) kerül, ahol tulajdonképpen már megfelelő szemcsenagyságú, szárított fűrészpor várja pelletálást. A silók és csővezetékeik – tekintettel az esetleges porrobbanás lehetőségére, illetve a finompor környezetterhelésére – rendelkeznek saját szikraoltó, tűzoltó és sűrített levegős szűrőtisztító rendszerrel is. Mindezek mellett, mivel a fűrészpor hajlamos a boltozódásra, saját bolygatóművel és kitárazóval vannak felszerelve. A fűrészporsilóból csigás anyagtovábbítóval (pos 11) kerül az anyag az előkeverőbe (pos 12), ahol megtörténik a homogenizálása, illetve szükség esetén az anyag vízpermettel, esetleg vízgőzzel való kondicionálása, amennyiben a szárítás a célérték (10%) alattira sikerült. Innen általában egy körpályás anyagtovábbító (pos 13) hordja ki a présgépekhez (pos 14) az előkészített alapanyagot. A présgépekben történik a tulajdonképpeni pelletálás, ami 800-900 bar-os nyomáson, 130-160 oC-os hőmérséklet mellett megy végbe. A kör keresztmetszetű geometriai formát a présszerszám, az úgynevezett matrica alakítja ki, és a fenti nyomás- és hőmérsékleti viszonyok mellett megolvadó természetes kötőanyag, a lignin „ragasztja”, tartja össze a szemcséket a présből való kikerülés után. Az igen nagy préselési nyomást mechanikai úton állítjuk elő a 2. ábrán mutatott módon. Az alapanyag a matrica belső terébe kerül, ahol a forgó matrica magával ragadja, és a belső palásthoz közel (0,5-1 mm) állított görgők alá kényszeríti. A görgők a matrica palástján elhelyezett, megfelelően kiképzett furatokba préselik az alapanyagot, majd a külső paláston kibúvó rudakat a törőkések megfelelő hosszúságban darabolják (1-3 cm). Kiemelkedő jelentősége van a jó minőségű pellet gyártásánál a présfuratok és az alapanyag „összehangolásának”. Hogy ez mit jelent, azt a 3. ábra segítségével szeretném megmutatni. Az „X” metszeten látható, hogy a matrica falvastagságát két különböző átmérőjű furat töri át. Az egyik furat a belső palásttól egy bevezető kúp után 6 mm átmérővel indul, ezt nevezzük présfuratnak, míg a külső palásttól egy 7 mm-es furat megy szembe a présfurattal, ez a kivezető furat. A furathosszak kialakítása attól függ, hogy milyen fafajtából (kemény vagy puha) akarunk pelletet gyártani. A puhább fát hosszabb présfuratban, míg a keményfát rövidebben lehet a megfelelő tömörségűre préselni. A metszet mellett lévő táblázat sejteti, hogy nincs túl nagy „préshossz-tolerancia” a különböző keménységű fafajták, illetve ezek keverékei között, hiszen a legpuhább és legkeményebb között 10 db 1-2 mm különbözőségű préshosszúságú matrica rendelhető. Amennyiben túl rövid a préshossz, akkor nem lesz megfelelő tömörségű a pellet, esetleg az alapanyagnál kicsit sűrűbb fűrészport gyártunk. Ha viszont túl hosszú a présfurat, akkor azon túl, hogy jelentősen nő a préseléshez szükséges energiaigény, szélsőséges esetben az is előfordulhat, hogy belesül a szerszámba az alapanyag, amit aztán csak „kézimunkával” lehet eltávolítani. De térjünk vissza a technológiai sorhoz. A présekből kikerülő pelletet egy szállítószalag (pos 16) gyűjti össze, s egy porleválasztó és hűtő (pos 17) egységhez továbbítja. A hűtő fontos része a technológiai sornak, hiszen míg a kötőanyag (lignin) nem hűl le, addig a pellet nagyon sérülékeny: könnyen törik és porlad. Innen egy szállítószalag (pos 18) a csomagoló (pos 20) előtti pelletgaratba (pos19) szállítja a kész pelletet. A megrendelői igényektől függően a csomagolás történhet 15 kg-os zsákba, big-bag zsákba, illetve ömlesztve. A cikk szerzője a gyártási folyamat bemutatása után rátér a gyártás nehézségeire, amelyek főként a gyártás gazdaságossá tételéből adódnak. Ugyanis a gépek heti 7X24 órás használata lenne energiatakarékos, de ahhoz meg nagyon sok anyagra (fűrészporra) lenne szükség. Például egy 1,5 t/h kapacitású gépsorhoz napi cca. 50 t 35-40%-os nedvességtartalmú alapanyag szükséges. A cikk teljes egészében megtalálható a Víz, gáz, fűtéstechnika épületgépészeti szaklap XI. évfolyam 5. számában. Forrás: VGF online cimkék: | |